The refurbishment of New Court at Trinity College, Cambridge, by 5th Studio and Max Fordham set out to radically improve the comfort and carbon emissions of a Grade I listed building. Five years after its completion, 5th Studio director Oliver Smith assesses the lessons that have been learnt.
Originally rendered with Roman cement, the courtyard-facing facades have been re-rendered using a permeable hydraulic lime painted with limewash.
What’s the best way to retrofit our historic building stock? How do we balance conservation with improved environmental performance and user comfort? For Trinity College, an academic institution with a portfolio of nationally important listed buildings and a uniquely long-term outlook, these questions are of critical importance.
In November 2009 the college commissioned 5th Studio to undertake a comprehensive programme of restoration and repair to make New Court fit for purpose for the next 200 years. The broader aim was to set a standard and methodology for retrofit projects across the University’s estate and disseminate learning to the broader benefit of the heritage sector.
Designed by the architect William Wilkins some two centuries ago, New Court is a four-storey, Grade I listed, neo-Gothic building containing 169 student study bedrooms, offices and teaching spaces arranged around a central court. It is constructed from solid brick walls with single-glazed casement windows and pitched slate roofs. The river frontage is clad in stone, the court interior is rendered and the only publicly visible elevation – onto Garret Hostel Lane – is fair-faced brick.
The building has a long, proud history, with former residents ranging from Alfred, Lord Tennyson to the current Prince of Wales. But it had fallen a long way behind contemporary requirements of comfort and amenity, building regulations and safety standards, and was notoriously expensive to run. Damp, draughty and cold rooms at the lower levels meant that the heating had to be turned up high and run almost all year, leading to over-heating of the upper floors to such an extent that students kept their windows open all year round.
Our brief was to achieve compliance with building, fire and other regulations; fit completely new service installations; renew the facades and character of the court and rooms; and crucially, reduce energy use and carbon emissions in line with long-term global targets. The aim was to approach Passivhaus energy performance standards, setting an industry benchmark for sympathetic low-energy refurbishment of ancient college building stock.
A centralised plantroom efficiently provides heat and hot water and includes connections to the planned ground source heat pump.
Investigation, monitoring and research
As a Grade I listed building, any changes to the structure would require listed building consent, but it was clear that a conservation-as-normal approach would not be able to deliver the step change in comfort and environmental performance required.
Our approach to the conservation issues was to frame this in three key questions: What are the heritage values of the existing building and what are their relative significancies? To what extent will the proposals harm or benefit those values? Is any of the harm outweighed or balanced by heritage or other public benefits?
Paragraph 132 of the NPPF states that “clear and convincing justification should be provided for any harm to the significance of a listed building and that harm less than substantial should be weighed against the public benefit arising from the proposals.” Crucially, it goes on to state that “The conservation of energy is itself a public benefit.” In other words, in making a case to the local authority – who is responsible for determining the balance between perceived conservation harm and wider public interest – there is scope to challenge conservation orthodoxy in the interests of improved environmental performance. But the onus of responsibility for making a convincing case lies firmly with the design team and the client.
To build our case, we embarked on a three-year programme of analysis, researchand monitoring. 5th Studio carried out a comprehensive survey documenting what remained of the original structure as well as all subsequent alterations and establishing an interpretation of heritage significance that relied less on cataloguing fabric and features than on its essential character.
Working with Max Fordham, and referring to a ‘brains trust’ of advisers (Bill Bordass, Bill Gething and Brian Ridout), we led a programme of investigation, monitoring and modelling to gain a thorough understanding of the building’s environmental performance, including in-situ U-value measurements, hygrothermal gradient monitoring, airtightness and thermal imaging, air pressure testing, and on-site weather data collection. At this early stage, this was as much a research project as it was a traditional building project, and the College established a technical committee to scrutinise the methodology, outcomes and technical proposals that emerged.
En-suites inserted into the existing floor plate bring 21st century amenity to a Grade I listed building. In order to avoid adding to the moisture load, shower rooms have been positioned away from external walls.
Fabric first
The primary challenge was upgrading the thermal performance of the building envelope. Adding external insulation to the listed facades was not an option – their historic character and status clearly called for a straightforward conservation approach. But the interiors, which were mostly pretty plain and had been subject to continuous ad hoc alterations over the years, were considered less sacrosanct. Hence we concentrated our efforts on exploring options for insulating the inside face of the exterior walls. This raised challenges of its own, not least the risk that insulating the interior faces of external walls could lead to interstitial condensation and mould growth. The brickwork walls not only housed joist ends and joinery grounds, but – as in other examples of early 19th century mass-brick construction – solid timber wall plates at four foot intervals all the way up the building. The College had addressed a substantial dry rot outbreak in the ground floor of the building in the 1970s, following the introduction of central heating, and was anxious not to have to repeat this.
Max Fordham used a modified form of the hygrothermal modelling tool WUFI to develop a clear picture of the way heat and moisture moved through the historic walls. This was calibrated against insitu measurements of moisture and heat levels within an existing wall by ArchiMetrics, giving a benchmark for assessing subsequent performance throughout the seasons and predicting the relative performance of different insulation strategies using varying thicknesses of insulation and vapour barrier locations.
Phenolic foam insulation gives the highest insulation levels for the least thickness, but is impermeable both to the outward movement of internally-generated moisture and the internal movement of water or solar-driven vapour leading to high levels of interstitial moisture (and mould risk) at the interface of the brickwork and the impermeable insulation.
Extensive modelling suggested that it would be preferable to line the walls with a plastered 60mm-thick vapour-permeable Pavatex fireboard insulation system to give a U-value of 0.25W/m / C and to do without a vapour barrier entirely, reducing heat loss while still allowing vapour movement through the insulation. Shower rooms – areas of high moisture generation – have been positioned away from external walls to avoid adding to the moisture load.
Rather than use a modern airtightness system of membranes and tapes to deliver the airtightness target, we adopted the low-tech, but more reliably deliverable approach of using a breathable, lime render coating to the inside face of the brickwork. This could be worked down into the floor voids and joist ends (where the biocidal properties of lime would inhibit potential mould-growth) and, critically, lay behind the insulation and lining layers where it would be protected against accidental damage by finishing trades or occupants.
Attic room ceilings had no insulation at all. Since the original lath and plaster had long since been replaced with gypsum and metal lath, these ceilings were deemed to have little heritage value, making it possible to for them to be remade with rigid insulation between and below the rafters achieving a U-value of 0.15w/m / C and airtightness of 3.0m3/h/m2@50Pa.
Much of the building’s original timber floor had been replaced with concrete in the 1970s. External ground levels had risen over time and the original lime-based renders had been replaced with Portland cement render causing rising damp from ground and surface water, as well as leaking drains. This was addressed by reducing external ground levels, improving drainage, and restoring vapour permeability to the restored and newly insulated walls. The 1970s ground slab and any surviving timber floors were replaced with a modern slab laid on rigid foam insulation and isolated from the walls by perimeter insulation.
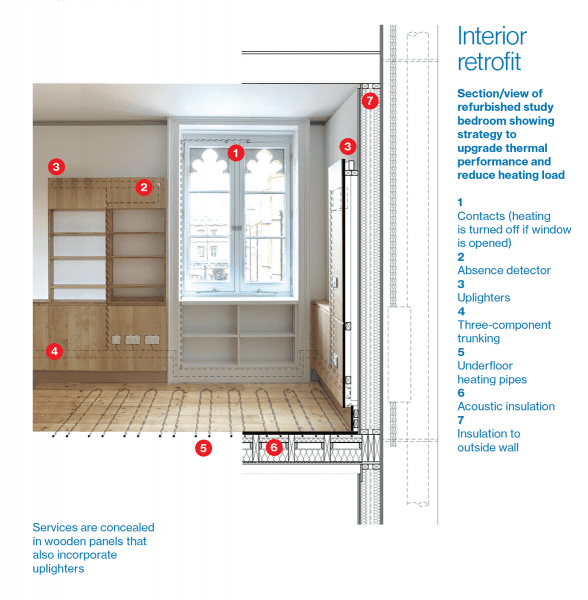
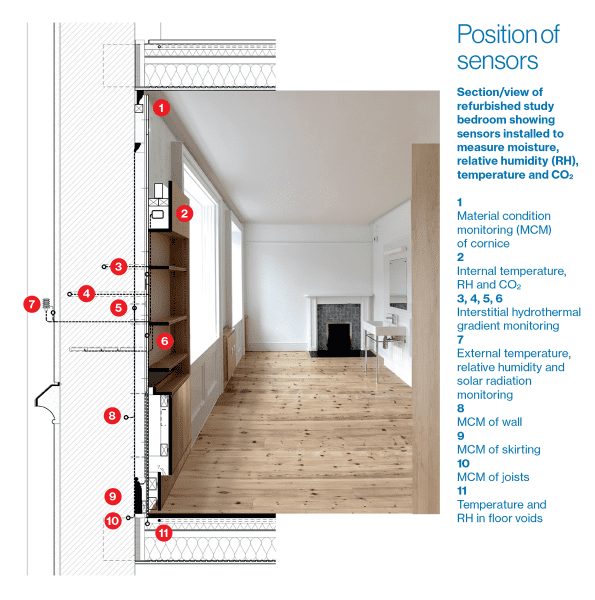
Windows and shutters
The design team explored a range of options for minimising heat loss through the building’s sash and casement windows. The timber-framed windows were 19th century replacements for the original metal-framed windows. Nevertheless, Historic England would not permit replacement with new triple-glazing, and objected to proposals to fit draught proofing and reglaze with 10mm double-glazed modern sealed units from the Holloseal range with rippled heritage glass as the outer leaf.
This departure from conventional conservation orthodoxy was approved by the City Planning Committee following an exhaustive exploration of the alternative options, the installation of prototype frames and glazing within one window in the court, and the demonstration that upgrading the windows was not a standalone item but an integral part of the overall fabric improvement strategy – without which heat demand would be so great as to make other components of the retrofit (MVHR and renewable heat sources) unworkable.
As well as reducing heat loss, the work to the windows was critical to reducing air permeability to 3.7 m .m-2.h-1 @ 50 Pa.
Glass from the existing windows was saved for use in the repair of windows elsewhere on the university’s estate. Timber casements, window shutters and architraves were skilfully repaired and altered off-site to accommodate draught and weather seals and the deeper glazing units, and repositioned in the openings to accommodate security fixings and to allow the newly installed insulation to run behind the shutters into the reveal.
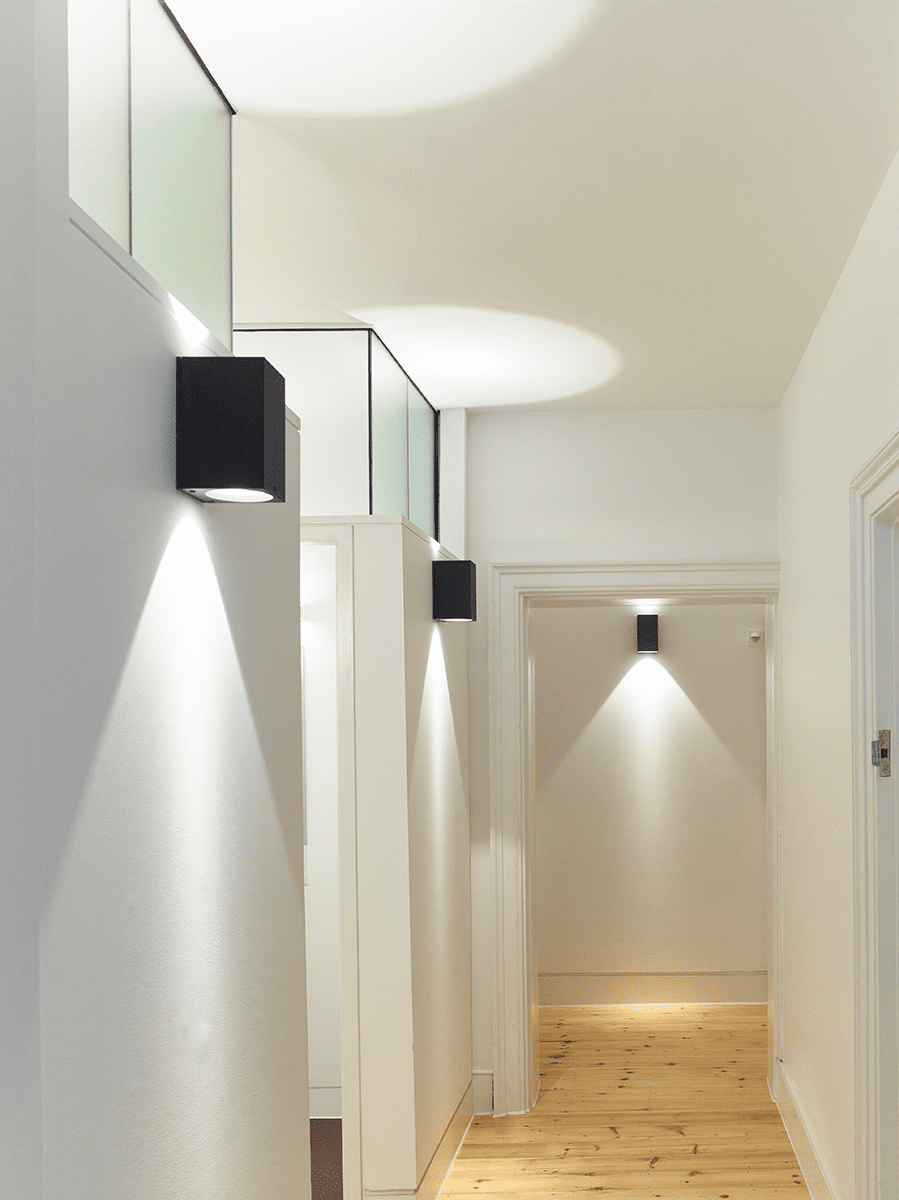
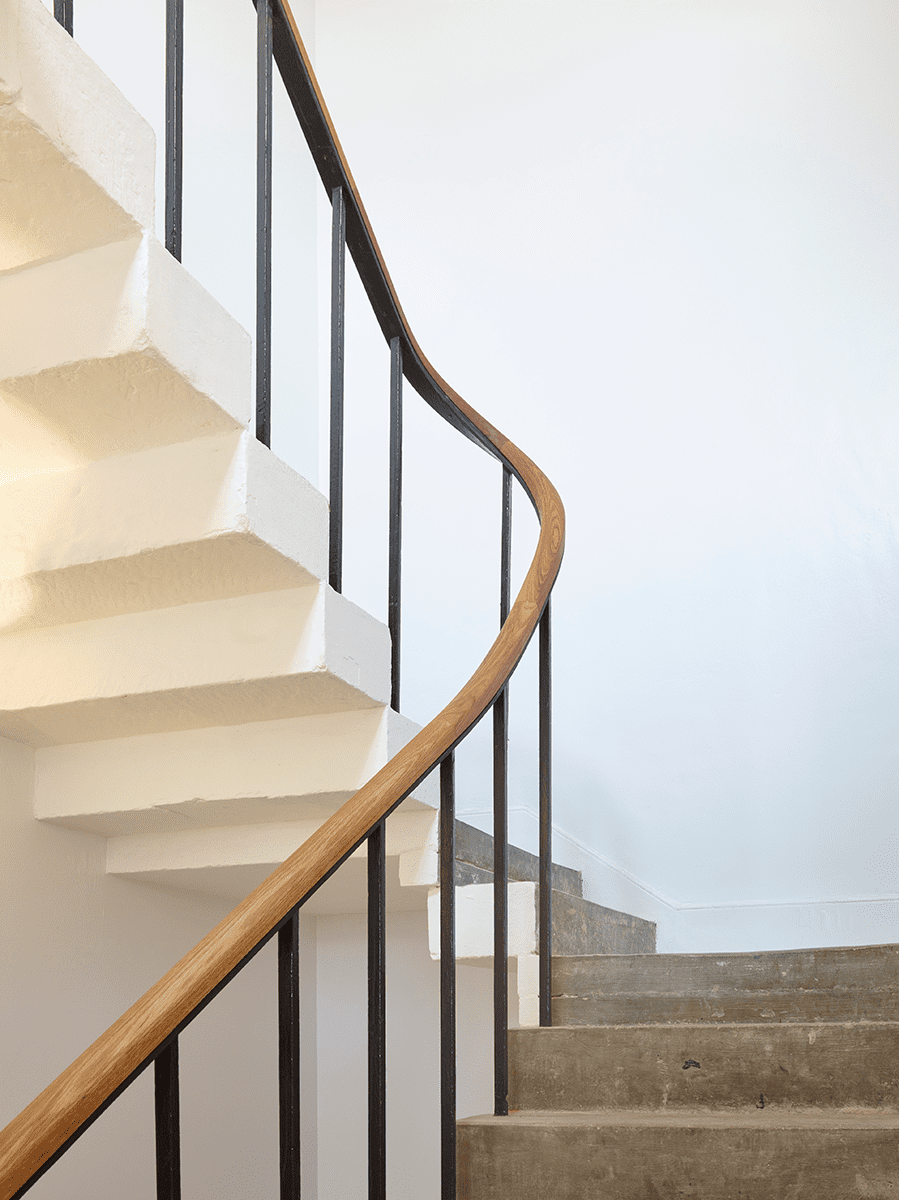
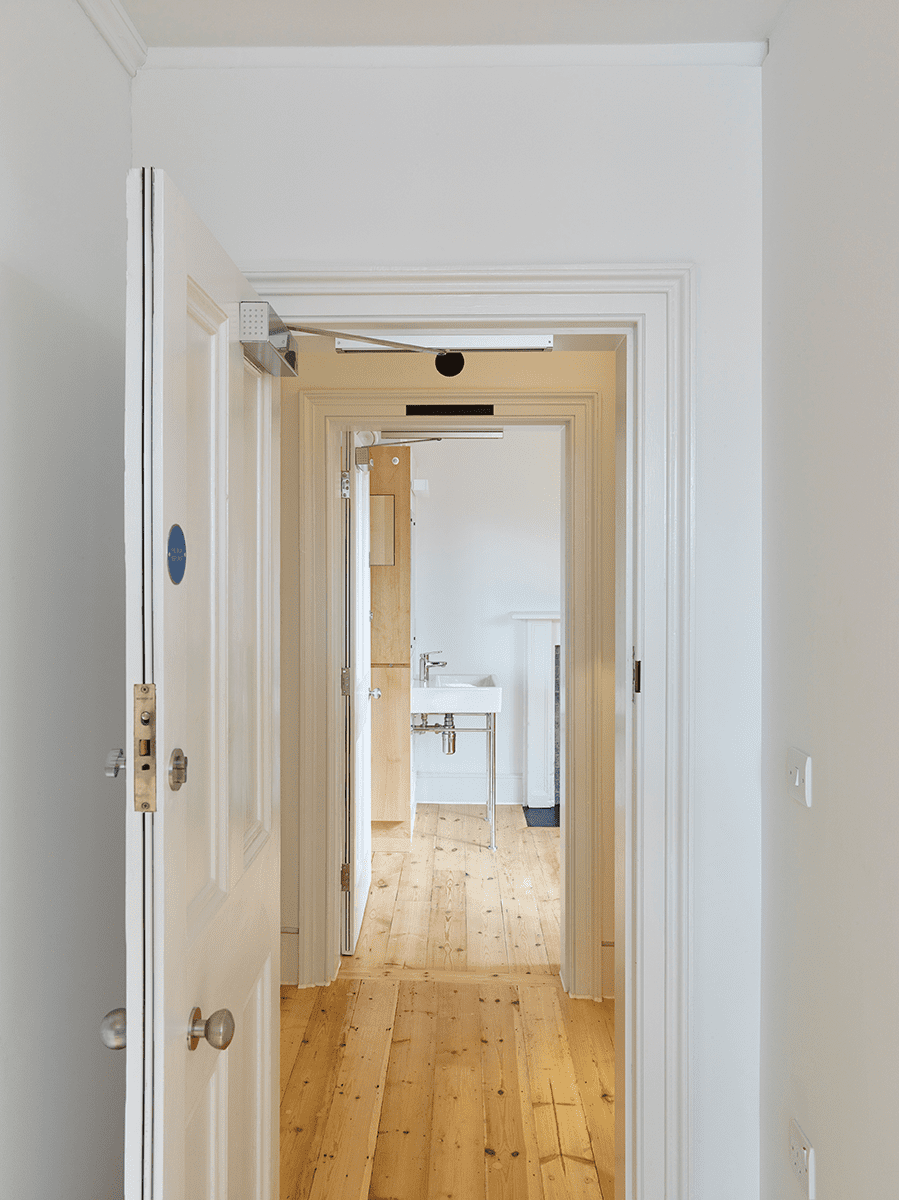
Interior fit-out
While the building’s facades have been refreshed but unmodernised, the interiors, particularly the student rooms, have been brought up to date with an architectural language that marries the historic setting with a more contemporary character. We took the decision to terminate the insulation and replastering just below the original cornices when thermal modelling indicated that this would have minimal impact on heat loss or on the creation of cold bridges and condensation risk – resulting in what was accepted as an ‘honest’ retrofit approach where the addition of a new lining to a historic shell defines the character of the room. The contemporary character – and warmth is expressed by bespoke timber fittings designed by 5th Studio, including bookcases, storage units and wall panels that conceal services, eliminating the need to chase cabling into walls.
Heating and ventilation
The archaic central heating system was replaced with underfloor heating installed beneath the original Georgian floorboards and to be warmed by ground source heat pumps. Rooms are generally maintained at 21 C, but occupancy sensors keep energy consumption to a minimum. The temperature is automatically reduced if a room is unoccupied for more than two days. Sensors in the window frames also ensure that the heating is turned down when the window is open for any length of time during the heating season.
The existing chimney flues have been used to provide heat recovery mechanical ventilation with one duct supplying tempered fresh air to student rooms and another extracting stale air from the stairwell, bathrooms and WCs. A heat exchanger in the roof heats incoming fresh air depending on the time of year. Photovoltaic solar cells are to be installed on south-facing roofs.
Delivery process
The project was delivered under a standard JCT contract, and completed in two phases over 18 months with 5th Studio maintaining a daily site presence throughout.
We found that the levels of site supervision required greatly exceeded the contractor’s expectations and that the combination of simultaneous work in multiple rooms and the degree of sensitivity, precision and craftsmanship required led to a great increase in the level and attentiveness of site management staff.
We also found that in the UK, construction trades are more focussed on skills and materials required for new-build housing than for retrofit works, and that there was a significant unfamiliarity with the processes required on New Court. This was addressed by the availability of suitably skilled subcontract staff largely from the EU (especially important in dealing with the lime render to the courtyard elevations), the main contractor’s willingness to adopt a process of ‘toolbox talks,’ rigorous quality reviews of all work, and our continuous presence. It is yet to be seen how these skills shortages will be addressed with the departure of many skilled EU trades, post-Brexit and mid post-Covid.
Lessons learnt
Five years on from completion, the building has delivered on our expectations. On-going monitoring confirms that the integrated package of works has already reduced energy consumption and carbon emissions by 80 per cent. The imminent completion of the heat pump and ground source array will decarbonise the heat energy and further reduce carbon emissions. Just as importantly, post-occupancy surveys demonstrate a marked increase in student satisfaction, with 80 per cent of residents saying that they would recommend New Court to a fellow student and others volunteering ringing endorsements, including my personal favourite “I actually think it’s the nicest place to live in college.”
Clearly, it’s possible to find a balance between conservation and improved environmental performance and comfort, but it takes a significant investment in terms of resources and time. There are a few pointers for gaining listed building consent for projects of this type. First, know who and what you’re dealing with. Every project has its own social and political context. Make sure you understand it. Get to grips with all relevant stakeholders, guidance, precedents, organisations and policies. Get to know the people involved.
Second, know your building inside out. Make sure you understand its history and cultural significance, as well as its construction and performance. The best way to gain the trust of the people you’re dealing with is to demonstrate that you understand their building as well – if not better – than they do themselves. Model different options. Make a convincing assessment of the heritage benefits or perceived harms of different solutions, as well as the implications for environmental performance and comfort. The sheer volume of research and analysis undertaken at New Court was fundamental to our ability to argue our case and counter concerns.
We were hugely fortunate in having a client with the will and the vision to support this process. For the college and the wider university and city, with their culture of improvement and learning, and an extensive portfolio of listed buildings, the benefits were clear. The development of a successful methodology for this research and design process – now embodied in the City Council local plan policy for historic buildings – has made this process faster, more incisive, and more efficient on subsequent projects.
If we are to upgrade our listed buildings at the pace and scale required it’s essential that we find ways to share protocols and methodology, but also to monitor performance, gather feedback and share lessons learned. One condition of being granted listed building consent was that Trinity College would undertake to monitor and report on moisture levels within the fabric for the next seven years. This is being undertaken by ArchiMetrics, who is compiling a body of data that can inform similar projects. For all its Gothic splendour New Court is straightforward in terms of construction, making the learning applicable to many buildings of a similar age both in Cambridge and across the UK.
Finally, don’t ignore input from heritage agencies and politicians. You don’t have to agree with everything they say, but it pays to make sure your listed buildings and planning applications are carefully curated to demonstrate that you have taken their input on board. Give their expertise and interest the respect that it deserves.
Lessons learnt from research
U-Value (ISO 6946) calculations are generally inaccurate for the performance of existing fabric. The varying density of historic bricks, the voids and rubble infill to walls all increase the thermal performance beyond the predictions of desktop software.
In the case of New Court, the average in-situ (ISO 9869) measured value of the old walls was 0.69 W/m2K against an ISO 6946 value of 0.94 – a discrepancy of 25 per cent.Failure to use in-situ measurements on other projects might lead to the use of greater levels of (inappropriate) insulation in order to reach modelled performance targets – with an associated increased condensation and mould risk.
Similarly, contemporary building material databases are predicated on the use of components that conform to current standards of regularity, dimensions, density, and performance. We found significant discrepancies in density, vapour and moisture transport coefficients between the bricks in the WUFI database and those measured from site materials (by Paul Baker and the team at Glasgow Caledonian University). This in turn led to a recalibration of the WUFI model.
Finally, we found that the role of weather and orientation can be as critical in establishing the building physics risk as the form of construction. Solar-driven vapour pressure in the summer can be a more significant factor than wind-driven rain over the rest of the year.
The standard modelling uses imported weather files and, in the absence of a working weather station in Cambridge, we found that the available Meteonorm data comprised the interpolation of data from three other weather stations each more than 40 miles away from the city and none of which shared a fen topography. As these were unlikely to reflect the particular characteristics of the Cambridge climate and thus invalidate the modelling, the college paid to install its own weather station on the roof of a nearby building.
Lessons learnt
Post-occupancy monitoring has taught us these lessons:
• Breathable constructions are not only more vapour permeable, to the benefit of the comfort of fabric and occupants, but are intensely resilient. A tennis ball lodged in a parapet gutter outlet caused the gutters to overflow into the fabric below. The raised moisture levels were identified by the monitoring system (acting in an ‘early warning’ capacity) before the dampness was visible in the internal finishes. Once the overflowing was stopped, the monitoring system indicated that the wood fibre insulation, lime parging and breathable finishes had returned to their previous levels of moisture without any deterioration in finish or thermal performance.
• Airtightness can lead to overheating if windows that are designed to be fully opened for ventilation in the summer are installed with opening restrictors (in accordance with H&S policy). Even out of heating season, the circulation of domestic hot water through floor voids and panelling can add to heat gains that cannot be addressed by the MVHR or limited opening windows.
• Occupancy interfaces, including window contacts linked to heating systems, and thermostatic control of underfloor floor heating temperature, can be vulnerable to ‘hacking’ by intelligent occupants. These interfaces and building BMS systems require greater protection against tampering and alteration.
Credits
Architect
5th Studio
MEP and building physics modelling
Max Fordham
Contractor
SDC
Structures
CAR
Cost consultancy
RUA
CDM coordinator
Gleeds
Building performance research
ArchiMetrics
Specialist subcontractor
Munro – M+E Service
Building products
NBT
Windows
Mat Bateman
Lime render
AVV
Joinery
Cousins