Divya Patel Orbesen explains how the practice’s state-of-the-art Materials Research Centre (MRC) and Information Centre (IC) support its multidisciplinary project teams and the wider aspirations of the company.
Head of the Materials Research Centre and Information Centre, Divya Patel Orbesen (far left) pictured with MRC colleagues Helena Nicholson, Evdokia Angeli, Alice Richards and Justin Pho.
Founded by Norman Foster in 1967, Foster + Partners (formerly Foster Associates) is one of the world’s pre-eminent architectural practices with more than 1,900 employees operating from 16 locations around the globe. Over the last 56 years, the company has produced a seemingly endless array of ground-breaking and critically-acclaimed projects, including the Sainsbury Centre for Visual Arts, Norwich (1978), the Hongkong & Shanghai Bank Headquarters, Hong Kong (1985), the Reichstag, New German Parliament, Berlin (1999), Hearst Tower, New York (2006), and Bloomberg, London (2017).
The practice’s success is due in part to its organisational structure and the strength and depth of its knowledge base. Integrated design teams work hand-in-hand with specialist in-house departments, which cover multiple disciplines ranging from structural engineering and sustainability to interior and urban design. Providing complementary support for project teams across the whole of the London office and beyond is the Materials Research Centre (MRC), and the Information Centre (IC). Presiding over these important resources is Divya Patel Orbesen, who explains how they function and what roles they fulfil in the in the day-to-day operation of the practice.
3D printed polyamide by Aectual. Evdokia Angeli: “This bio-based 3D printed material can be used to form screens, acoustic panels and even floors. Made from plant oils, the product is carbon neutral, and 100 per cent circular, recyclable and VOC free.”
What is the Materials Research Centre and what is its main purpose?
First and foremost it’s a materials library with more than 25,000 samples. When we set up the MRC we questioned what format the samples should be in respect of ease of storage, aesthetics and handleability – before settling on A4. Larger items tend to be stored in our off-site model shop, but can be brought over to us very quickly when needed. These are often used in client presentations to convey the true scale and/or appearance of cladding materials and interior finishes.
Holistically speaking, it is an in-house information service on rational material selection and suitable manufacturers or suppliers, providing advice in line with local environmental conditions for projects around the globe.
To answer the second part of your question, I would say that the purpose of the MRC is to provide a knowledge base for the practice on everything material related, from products and technologies to processing and sustainability; it’s pretty broad-based. Day-to-day, we provide a service for the architects on anything that they might need in terms of material and product information. This can range from sourcing local materials that support the aesthetic of a competition-winning design, to researching how selected materials can be manipulated or processed to provide the necessary levels of performance required by our projects.
Himalayan Salt Brick by Saltan. Alice Richards: “As the name suggests, these stunning-looking bricks are made from salt, and are really only suitable for interior use, as salt is quite a reactive material. They have a very calming aesthetic and a wonderfully warm tone – especially when back lit.”
How is the MRC organised?
Spatially, its divided in two, with the ‘bread and butter’ materials, such as metals, woods, concrete, stone and glass housed in compact cubby holes on one side, and the more innovative and inspirational materials stored – and displayed – on the other. Each item, wherever it is located, has its own QR code, which corresponds to our online materials database. Materials and products relating to a specific project are stored in numbered sample trays, which are taken out of the MRC for design reviews and client consultations. At a wider scale, the MRC acts as a central resource for the whole organisation. We use a large plasma screen to conduct interactive discussions with our satellite offices if they are looking at particular materials and products.
How do you staff the MRC?
We have the materials librarians, consisting of Alice Richards and Helena Nicholson, who form the frontline in helping architects find a particular material. Then there are the materials researchers, comprising Justin Pho, Evdokia Angeli, Natasha Riedzua, and Corina Dragomirescu, who provide varying levels of in-depth technical research for material applications on specific projects.
With upwards of 1500 people in the London office, can anyone come into the MRC at any time?
Yes. Architects can use the facility at any time they want, although it can get very hectic. What I must say, is that the MRC is strictly a reference library! It used to be a borrowing one, but this became very difficult to coordinate as we have around 150 live projects at any one time. Unfortunately, it got to the point where a lot of the innovative samples were on people’s desks, which meant that the library could no longer help or inspire project teams in the way we originally intended. Added to this, the MRC contains a lot of cutting-edge materials from the aerospace, transport and yachting industries, which are unique and cannot easily be replaced if they are taken away and not returned.
WasteBasedBricks by Stonecycling. Divya Patel Orbesen: “These beautiful bricks are made from demolition waste (at least 60 per cent) and can potentially be used in conjunction with bio-based mortar. The company also produces brick specials, slips and tiles.”
What is the Information Centre and how does it complement the MRC?
Originally, the IC consisted of an extensive collection of product catalogues and technical literature, alongside architectural books and periodicals. However, as everything is now online, the IC is now a digital library containing manufacturer and product information, together with a wealth of technical data and regulatory guidance from organisations, such as IHS, BSI, TRADA and CWCT, to name a few. It also contains in-depth performance analysis related to past projects and research undertaken with our Technical Design Group. Overall, the MRC and IC support each other in their role of providing an information service and developing a knowledge base on current and new materials and products, technologies and sustainable and technical case studies.
There’s a vast array of incredible materials on show in the MRC. What is the process behind researching and finding them?
Through meetings with industry, attending trade fairs and educational seminars, the MRC accumulates, collates and condenses the latest in material and product technologies. Manufacturers and specialists frequently come to us with their latest products and innovations. We also subscribe to newsletters from companies we’re familiar with, and attend trade shows and conferences. Researching topics of specific interest to the practice, such as the life expectancy of bio-based materials, or the fire performance of different timber elements, provides another means of discovering new products, treatments and coatings.
What materials are currently inspiring you and your team?
One of the most interesting and unusual products is a 3D-printed building block made from sewage.
You’re joking?
I’m not. The material has obviously gone through a thorough process of decontamination, but if you think about it, there are eight billion people on earth, so printing and building from human waste has huge environmental potential.
M3D printed sewage waste by Omlab. Divya Patel Orbesen: “Formed from a mixture of treated human waste, cellulose, calcite and water, this sustainable and biodegradable 3D printed product can be used to form non-loadbearing walls. They are currently working with concrete companies to see if it could be adapted for structural use.”
What other materials are capturing the MRC’s imagination?
Another product that we love is Vantablack – the blackest material in the world. The coating is made from carefully arranged carbon nanotubes and absorbs more than 99 per cent of visible light. It makes 3D objects look 2D, so we’re thinking, if we used it in a ceiling, would the ceiling disappear visually?
We’re also focusing on brick innovation and have discovered a range of new products, including bricks made from salt and bricks which are designed to increase biodiversity by providing micro habitats for bats, bees and birds. The material will form the subject of our next in-house exhibition. Our current display is on PV and includes a ground-breaking PV cell by Ubiquitous Energy, which is completely transparent. Our intention with each exhibition is to disseminate the latest material developments and related technical research to the wider practice.
Natural materials and fibres, such as jute, rattan, bamboo are another source of interest currently, and we’ve got a new display bay devoted to them. It’s about sustainability and how could we use these products on our projects, while meeting the necessary performance accreditations and certifications.
Wooden Curtain by Elisa Strozyk. Divya Patel Orbesen: “Applied to textile-based backing material, these lazer-cut timber veneers can be made into complex three-dimensional shapes, which provides a lot of scope for innovation. They are currently being considered for use on several projects within the practice.”
You mentioned sustainability. How important are environmental issues when it comes to material selection?
The practice has always had a strong sustainability agenda, and in terms of materiality it’s about using only what is required and nothing more. Materials are a precious resource and should always be used efficiently and effectively. Recycling and reuse are clearly important, but the industry needs to step up and establish clear streaming routes for the myriad of building products that could and should be reprocessed. Lifecycle assessments of materials and environmental attributes are a fundamental aspect of any material or product related query.
Of course, some materials, such as reclaimed timber flooring, can be reused very easily, while others will require additional processing, and the question is: will they meet the necessary certification in order to do that? We’ve also undertaken a lot of research into how buildings can be disassembled and what can be done with the components in terms of reuse, upcycling and recycling. This is applied to our projects and is aimed at utilising and benefitting local waste streams and economies.
How important is making and prototyping in terms of material research?
Mock ups are very important to the practice and are frequently constructed and/or housed in the MRC. An example is the origami-like structure made from Tyvek breather membrane, which is suspended from the ceiling. We collaborated with the company that produces this unusual product with the aim of creating an illuminated, sculptural screen or ceiling raft.
So this was a research exercise, rather that something for a specific project?
Yes. It was seeing what we could do with an innovative product. We also experimented with dichroic film to see how these kinds of structures might reflect the light. Ultimately, it’s about testing ideas and inspiring the project teams. The MRC is not purely a functional amenity, it’s also about stimulation, inspiration and expanding the notions of what is possible, which is central to the ethos of the practice.
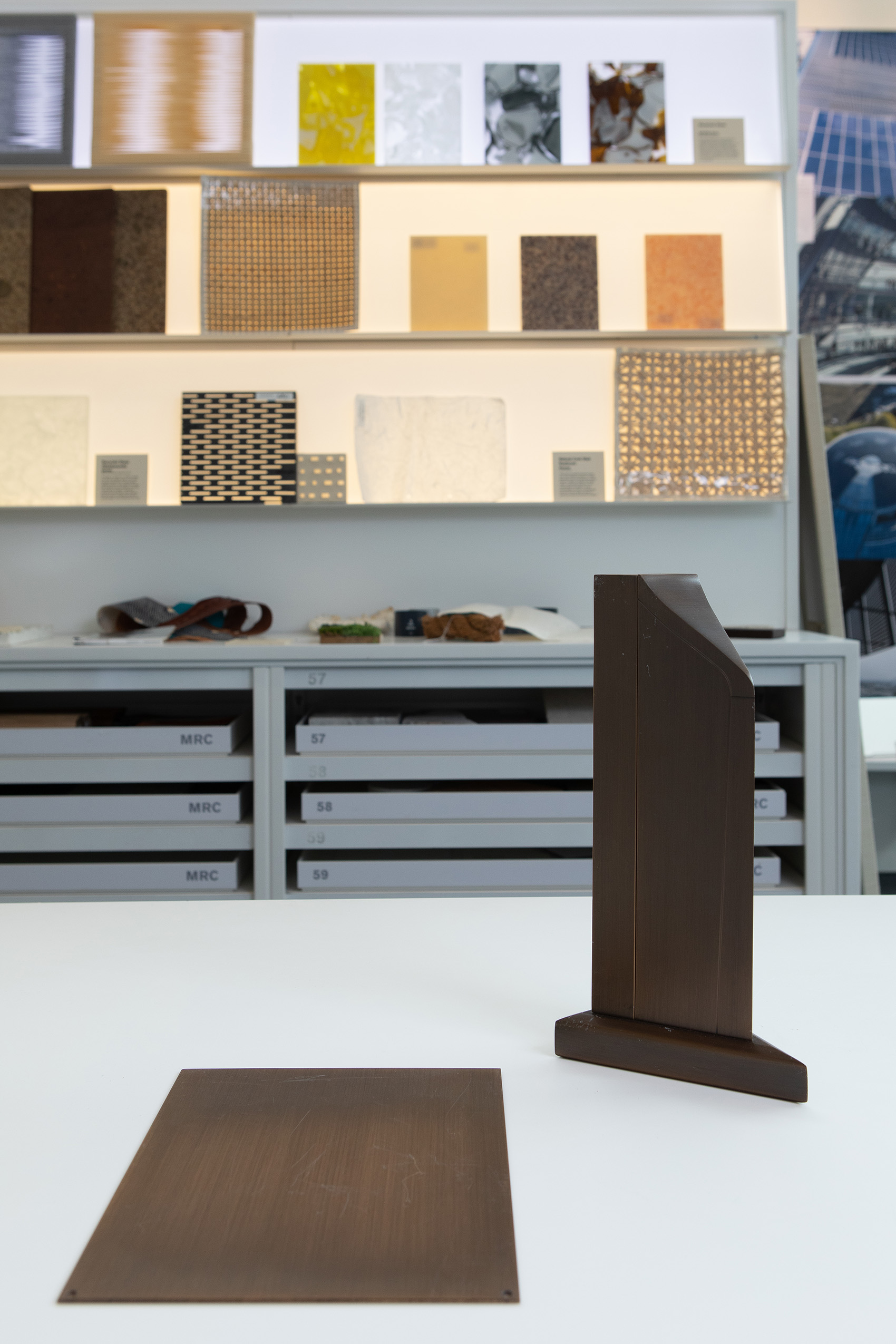
Bronze alloy sample and mock-up section of Bloomberg cladding fin by KikuKawa. Alice Richards: “KikuKawa has an amazing range of bronze alloys – among other metals – and one of these was selected for the external fins on Bloomberg. The company was also responsible for fabricating the fins and ensuring that the bespoke surface finish was fit-for-purpose.”
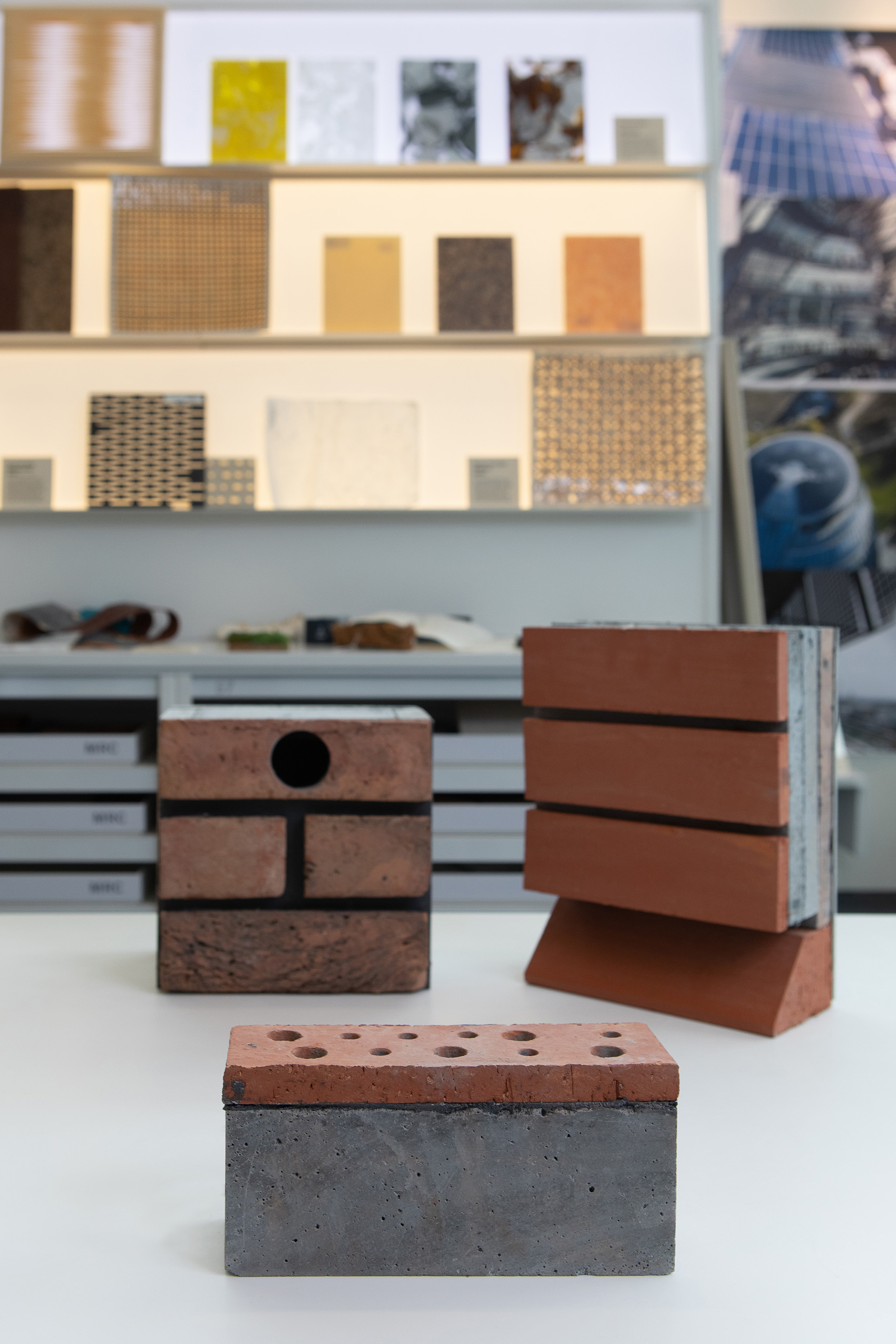
Bee Brick, Bat Brick, and Eco Habitat Brick by Wienerberger.
Helena Nicholson: “We like these innovative brick-based products for their ability to boost biodiversity and the way in which they can be seamlessly integrated into the fabric of the building. Brighton & Hove Council recently stipulated that all new buildings above five metres should include bee bricks.”
The MRC seems almost like a world within itself
It is and that’s what we love; we get to play with materiality and learn about it first hand. We also provide workshops, CPDs, and as I already mentioned, exhibitions. We pass on our knowledge, research and excitement about materials to the rest of the practice. CPDs are videoed, so they can be shared over the office intranet.
How do decide which CPDs to run?
They often relate to subjects that the MRC is being asked to research. We also get a lot of innovative companies approaching us with their CPDs. Recent events have covered recycled façades, fabric façades, ceramics, glass craft and technology, clay plasters, and non-toxic fire retardants.
What is your approach to working with manufacturers when developing materials or products for a specific project?
We frequently ask manufacturers to ‘tweak’ a particular product in order to suit a specific application. This can relate to both aesthetics and performance. A good example is BYO Living who make rattan screens, among other products. We were looking to use their screens on the interior of a large office building, but the requisite fire performance couldn’t be achieved. So instead, BYO Living made the screens from additive added recycled plastic to our original design specification. The finished product is on display in the MRC.
3D printed sand by Sandhelden. Justin Pho: “This is a fascinating material with a lot of potential, although we do have sustainability concerns relating to world-wide sand consumption by the construction industry. However, the company has agreed to work with us in exploring the potential of using desert sand instead of excavated sand in the printing process.”
How important are factory visits?
They’re very important. It’s only when you see the machinery and the production processes first hand, that you can understand the limitations of the material and what is and isn’t possible in terms of manufacture. It’s generally architects who undertake the factory visits, but MRC staff sometimes attend if they have been closely involved in the developmental stages of using a certain material or technology. Manufacturers are increasingly posting YouTube videos of their production processes, which form another useful resource for our design and MRC teams.
What happens to materials and samples at the end of projects?
We try to keep a reference of everything architects could need in the MRC. But of course, they work closely with manufacturers and suppliers, so by the end of their projects they will have a range of bespoke samples. We will look at these, and where appropriate select them for inclusion in the MRC collection. Control samples from every project are logged and stored by our Facilities team in long-term storage.
How do you reduce waste?
In general We’re finding that manufacturers are increasingly willing and able to take back samples that are no longer required. Kvadrat for example, takes back its fabric swatches and recycles them. What we’ve also done is collate items that are no longer needed or can be sent back, and hosted reuse-recycle events where the architects and other members of staff can take want they want for private use. People here are very creative and can spot opportunities for repurposing surplus items.
Curved Travertine by Atelier Romeo. Divya Patel Orbesen: “Made from waste stone and resin, this innovative material has many potential uses – not least for lighting due to its hollow form.”
With so many items stored, how do go about reviewing the library?
As I mentioned earlier, every item in the MRC has a QR code, so we know when it is due for renewal.
By renewal, do you mean a date when the product is due to be superseded?
It works two ways. The manufacturers themselves know what they have here and will let us know when certain products have become redundant or no longer manufactured. Other products, such as metals with traditional finishes or coatings, do not tend to change, so we review these less often, and will generally only update them if the sample itself has has become worn or discoloured through handling. It’s important to keep up to date when you are dealing with such a large resource of samples.