80% House by Prewett Bizley Architects
The Architecture Today Editor’s Award for contribution to shared learning went to 80% House, the deep retrofit of a London terraced house. Robert Prewett discusses the lessons learnt from 12 years of POE.
Editor’s Award
Front elevation viewed from the street. Credit: Killian O’Sullivan
In June 2007, Prewett Bizley Architects was focused on new-build multi-dwelling projects, as we thought that this was where sustainable architecture was headed, and we were deliberately turning away ‘back extension’ schemes. So when we were approached about this Victorian terrace refurbishment in a conservation area in Hackney, east London, I was about to politely decline, when the words ‘deep retrofit’ were mentioned. I paused and was intrigued as until then our ambitions with energy efficiency and existing buildings had generally been met with disinterest. My NO became a YES.
In fact, alongside a desire for some modest extensions, our client wanted to reduce the energy consumption in line with the Kyoto Protocol ambition of 80 per cent. While this seemed possible – based on some early calculations – there was very little precedent and we were told by many that it wouldn’t work, wouldn’t get planning, wasn’t buildable, and was a waste of time.
Axonometric drawing showing the principal environmental design strategy for 80% House.
Nevertheless, we came up with the following strategy:
- Create compact extensions presenting as little external envelope as possible.
- Cover the front of the house with a thick layer of insulation built up as series a of layers, including a ventilation gap between old and new to manage moisture risks.
- Replicate multi-pane sash windows using the best available thin double-glazing with quadruple draft proofing.
- Rebuild the rear façade as thick cavity wall (due to extensions and the dire structural condition of that wall) reusing original brick, with triple-glazing from Germany to all openings.
- Rebuild the roof as a warm roof forming a new extension with an EPDM covering.
- MVHR (mechanical ventilation with heat recovery) and boiler located in the roof extension.
- Underfloor heating on the lower-ground floor and one bathroom radiator on first floor as the entire heating system.
- Shading to loft windows by blind and to the lower-ground floor by pergola.
Following an excruciatingly slow planning process that lasted most of 2008, the project was constructed during 2009, and then occupied from early 2010, where monitoring began.
There are five key lessons from our POE on this project:
1. Fabric retrofit without a performance gap is possible
Figure 1. Bar chart showing annual energy use before and after the works, as well as the modelled proposal.
The left bar in Figure 1 represents our estimate for energy use before the works. It was modelled using SAP software and checked against real publicly available energy data for similar neighbouring houses. Typically the heating load dominated.
The modelled proposal is shown by the middle stacked column, where the heating has been slashed to the point where it is similar quantum to the heat wasted by the boiler due to flue losses in the ‘before’ case.
The third column summarises actual energy use measured at the meter following the work. The similarity to the middle column prediction is uncanny. It is in fact more commonplace for one to find a performance gap between modelled and measured results with measured invariably being higher than modelled (by as much as a factor of two or three). We attribute this lack of a gap to the care taken in the design and construction of the continuous thermal envelope and the attention paid to airtightness.
2. The fabric efficiency has not deteriorated
Figure 2. Bar chart showing recorded annual energy consumption from 2011 to 2022.
Figure 2 plots the energy consumption each year following completion. While there are differences due to occupancy and weather variations, the energy consumption and generation is remarkably constant from year to year with no overall trend upwards or downwards. This degree of stability strongly indicates that that the energy-efficiency measures have all held up and not degraded. This also indicates a lack of ‘rebound effect’, where energy-efficiency measures might be used to maintain an improved level of comfort at the expense of intended energy reduction.
3. High comfort
Figure 3. Graph showing recorded average indoor and outdoor temperatures from December 2016 to March 2017.
Internal versus outdoors temperature was recorded during winter 2016/17 (Figure 3). The near 20°C (owner-set), remained very stable except during vacant periods when the heating was turned off. Despite just two heat emitters, the rapid recovery upon reoccupation is noteworthy and encouraging.
Figure 4. Graph showing recorded average indoor and outdoor humidity from December 2016 to March 2017.
Relative humidity was also recorded as a ‘proxy’ for air quality (Figure 4). Readings were mostly within the ‘ideal’ 40-60 per cent bandwidth, which is preferred because it creates unfavourable conditions for dust mites, fungal spores, and bacteria proliferation.
Figure 5. Graph showing recorded CO2 during March 2023.
CO2 concentrations were also tracked for a shorter period (Figure 5). The count generally varied between 400-600 which is especially low and only once reached the upper limit of 1500ppm, beyond which air quality is by convention normally deemed poor. This occurred when the ventilation system was switched off for airtightness testing, and is not therefore representative of day-to-day conditions.
4. Retrofit can be done safely and responsibly
Over 13 years, the building’s fabric and environmental conditions were periodically examined with a final review study in March 2023. Air tightness, thermography, and mould spore detection revealed minimal defects, except for a leaking cistern valve (rectified) and some local rot in one window frame. The energy-efficiency work showed no specific issues, underlining the house’s positive performance with minimal maintenance over 13 years.
5. Lifetime carbon very attractive too
Figure 6. Graph showing whole-life carbon comparison of existing house versus completed retrofit project.
Shortly after completion an embodied carbon assessment was carried out which indicated an overall ‘spend’ of around 32 tonnes (266 kgCO2/m2), way below the RIBA 2030 recommendation for new build of 625 kgCO2/m2. Figure 6 compares the total carbon (operational and embodied) over 60 years for the pre-retrofit dwelling (in red) and the post- retrofit dwelling. While the ‘carbon burp’ associated with the works sets the retrofit ahead initially, its much lower operational emissions mean that the embodied spend was ‘paid back’ in around 7-8 years. Since around 2017 it can be seen to be saving carbon.
There are some things we might do differently now:
- When working on traditional buildings we now commonly specify ‘moisture open’ (hygroscopic and capillary active) insulation in order to reduce moisture risks generally. This may result in a slighter worse U-value but we find the long-term benefits of the material compatibility with the original fabric very attractive.
- Glass technology has evolved a lot. The latest commercially-available evacuated glass allows convincing replica sash windows to be produced now with a U-value close to 1.0, compared to around 2.3 for our attempt in 2008.
- We only used two heat emitters and expected the MVHR to even out temperature across the house. That was a bit naïve really, and while the client is quite happy with controllability of the house, we now design in more controllability.
- As summers have brought more extreme heat we have become increasing cautious about large areas of unshaded glazing particularly on western façades. We would now almost certainly recommend external shading to the rear windows at upper ground level. We would probably have a slightly reduced area too, with glass specified to better balance heat loss and heat gain.
Credit: Killian O’Sullivan
For future projects we have developed a number of precepts which are rooted in our learning on this project:
- We see value is almost all built things now in a way we did not before, and generally seek to demolish as little possible, focussing on optimising whole life carbon.
- This principle extends to thinking very carefully before proposing extensions. If we can make the existing accommodation work hard enough to satisfy the brief, then generally we avoid new building proposals, particularly where structural works involving steel and concrete are likely to be involved. We see small as normally better with less cost, less carbon and with smaller building envelopes requiring less heat anyway.
- We think about heating very differently now. In 2008 gas was the cleaner energy but as the grid has decarbonised, electrification of heat is now the winner. Heat pump efficiencies make this doubly attractive. We now consider the heating system alongside the fabric efficiency measures at feasibility stage and seek to optimise how each can magnify the impact of the other. Instead of ‘fabric first’ our approach is more ‘fabric and….’
- We have also started to experiment with cooling using heat pumps running in reverse in summer. For urban heat island locations, we believe that such active cooling for a one ‘retreat room’ at least is likely to become increasingly necessary even when excellent passive measures have been designed in.
In 2008, sustainability in construction was dominated by standards like the Code for Sustainable Homes for new-build work. Retrofit was not really recognised as an important endeavour and was hardly even a recognised term. A decade or more later we have come to realise that it is how we manage our existing buildings that will really make the difference. Figure 7, which is based on UKGBC data, indicates just how important retrofit ( shown in purple) is for the built environment.
Figure 7. Graph based on UKGBC data demonstrating the importance of retrofit in terms of achieving net zero by 2050.
I hope projects like this demonstrate that ambitious targets can be met and can yield very attractive outcomes, even for properties which have considerable constraints. The number of properties to deal with remains daunting, but if every refurbishment, every maintenance programme, and every estate regeneration has energy efficiency built into it, then I am more hopeful now that I was in 2007 that our built environment can each net zero in time.
Additional images
Our awards sponsors
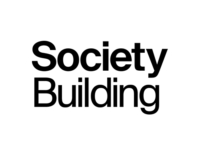
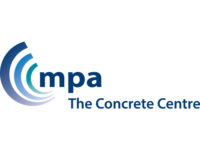
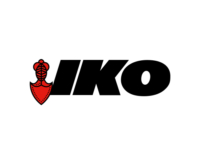

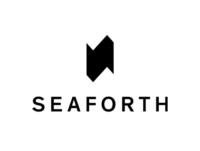
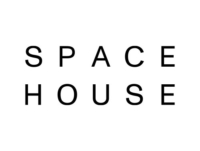
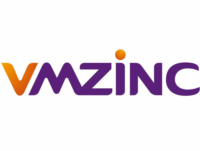