Richard Dudzicki of RDA Architects has converted a 19th-century brick workshop from his practice’s office into a home for his family and a contemporary addition to the Victorian street. He describes the challenges involved in working towards EnerPHit standards to reduce energy consumption and create a comfortable environment all year round.
The project included adding another floor on the roof and extending the ground floor.
The average house in the UK consumes 177 kilowatts per square metre per year (kWh/m .a ). The eco-friendly homes we were designing even 10 years ago have an energy consumption of 15 kWh/m .a, less than a tenth of this amount. Aside from the huge reduction in energy consumption, Passivhaus offers significant improvements in quality of life. I have spent the last 12 years persuading clients of the benefits of Passivhaus: natural filtered air, no drafts, outstanding sound insulation as well as the environmental gains. So when my family outgrew our two-bedroom home, my two teenage kids challenged me to practise what I preach and deliver a Passivhaus home.
The site, in East Dulwich, London, was a 120 square metre 120-year old commercial timber yard surrounded by nine other buildings, some in multiple occupancy, and accessed by an alleyway which runs alongside a sub-station. We set ourselves the challenge of using the existing fabric to create a four/five bedroom family home that would meet EnerPHit standards, the Passivhaus retrofit equivalent, working alongside other consultants such as CTC Engineers, Ecospheric and Mead Consulting as a certifier to help us along the way. Our approach was to construct a building within a building; to line the existing structure with a steel frame, put another floor on the roof and dig out the partially existing basement to create more room at the lower levels, primarily for plant. We also decided to extend the building on the ground floor.
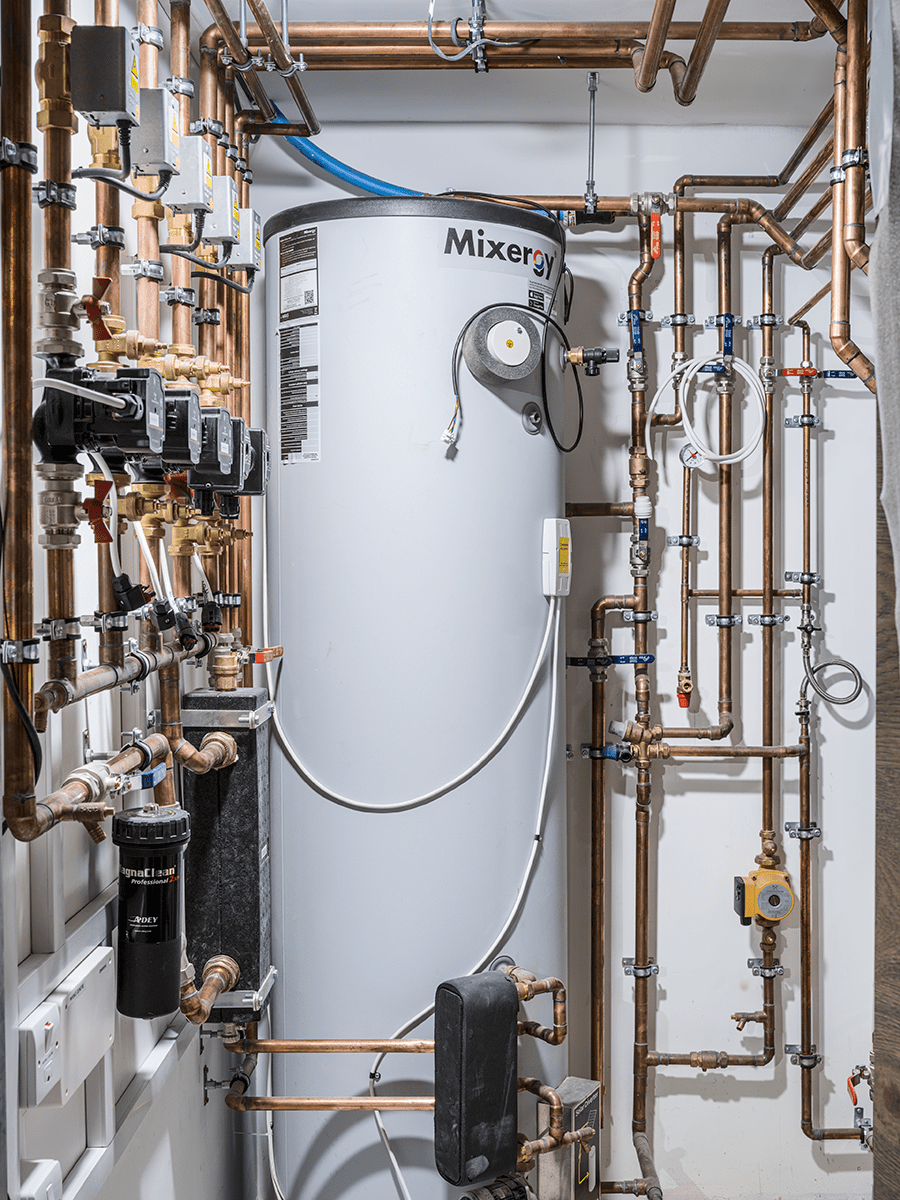
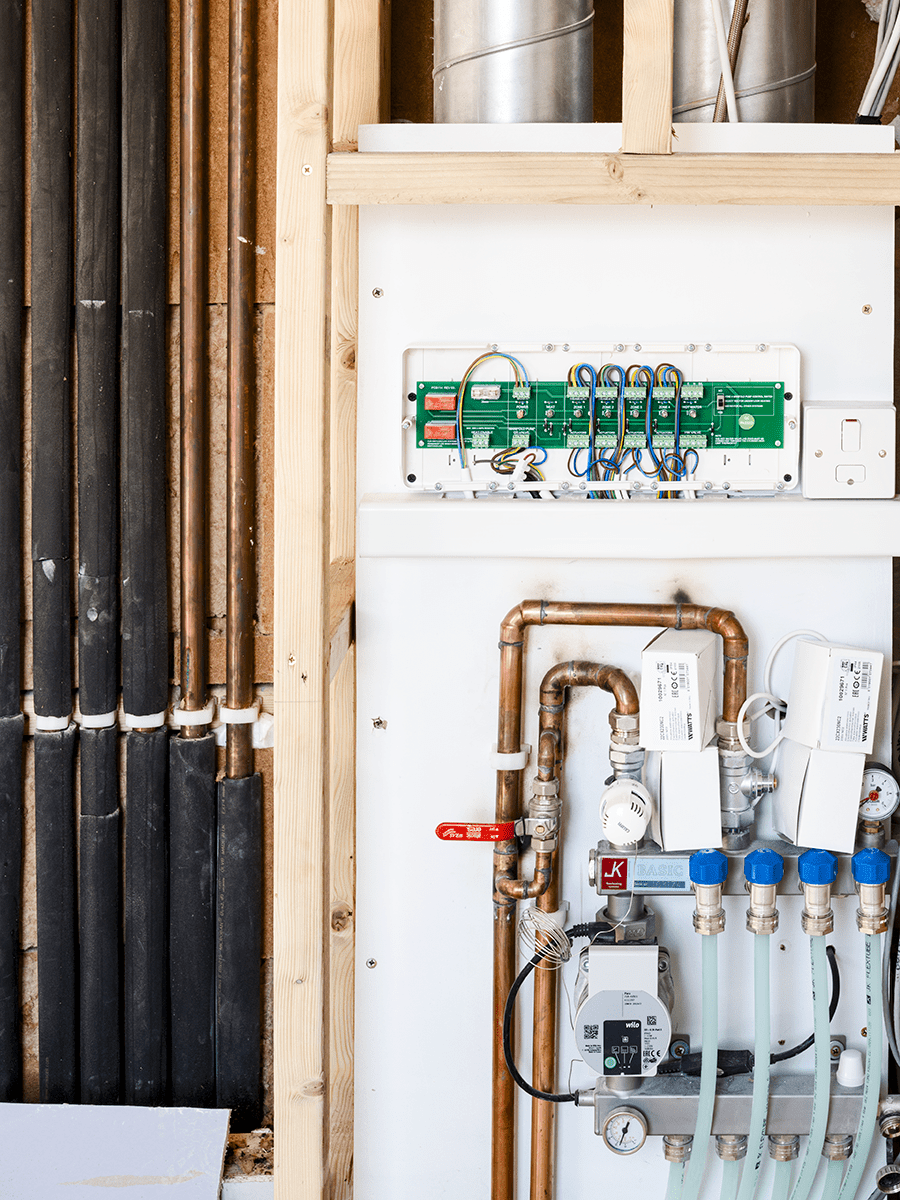
The main aspect of the building faces towards the south-west with very little light to the other elevations. This meant incorporating shutters in the south-west elevations to prevent solar gain and using skylights to bring light into all parts of the building. This would all be tested in PHPP – the Passive House Planning Package for residential building design and certification. The existing industrial window openings were kept, and a lighter scale of floor was built above the building with the circulation also acting as a light well.
The technical challenges were immense. Firstly, the steel frame could not touch the existing walls or floor slab as it needed to be separated to prevent any cold bridging. Working with CTC Engineers, we came up with the solution of using Farrat plates to separate any thermal bridging between the internal steel frame and the existing external brick walls. In some areas within the basement, we created fibreglass coverings by pouring resin over the top of the pads and over the Farrat plates. This would isolate the tanking membrane and the area that would be subject to damp on the steelwork.
The space behind the steel frame and existing brickwork was left at around 20mm wide, though this varied as the brickwork was in very poor condition. We used aerogel behind the steel frame to ensure that the steel frame was isolated from the existing brickwork. The steel framework, which is effectively three storeys tall, had to be braced back against the wall. M12 bolts went into resin anchors in the wall, then Farrat plates were placed around the bolts and structure. The original London stock walls were repaired and stitched where necessary.
One of the weaknesses we had when carrying out the works was we did not carry out a full cloud-based point survey and some of the walls were leaning into the building far more than the engineer liked. Certain sections of the first-floor top walls had to be rebuilt. The internal wall was given a coat of lime render as a parge coat, using Ecocork from Mike Wye. This would allow the walls to breathe as we were concerned about interstitial condensation. The inner walls were lined with 120mm of Steico wood fibre insulation, ready to be finished with lime render and an Ecocork render, which will become the finished internal wall finish once painted with a Graphenstone paint. We specified Magply tile backer board in the bathrooms as this allows for the necessary breathability.
Great care was taken while making the steel frame to ensure all of the routing and correct ducting was considered for the MVHR unit. We selected the Renson Endura Delta MVHR system. This was designed so that the air handling would occur by the front door within a grille unit, rather than an ugly ventilation pipe. The MVHR unit was placed in an area below the front door to keep the ducting as short as possible to the external wall. The riser serving the rest of the house is central to the building and then spiders off to each individual room.
Raising the roof
Once the steel frame had gone in and the floors were laid, the barrel-vaulted VM zinc roof, which would give the extra floor, was put in place. The beams were made out of laminated and glued structural grade plywood, which was cut out at a local joinery workshop, minimising the complications of waiting on delivery – a key consideration during the pandemic.
The roof structure was then covered with ribs, very much like an aircraft wing, staggered, filled with wood-fibre insulation and lined with plywood skins to create a diaphragm. This added to the strength and robustness of the steel frame.
Upstands were made for the Passivhaus Velux windows, which were insulated to allow for a zinc barrel-vaulted roof. The inside of the barrel vault, once it was lined with the plywood, was painted and sprayed with Passive Purple and we used air tightness tapes around the roof structure, the window frames, as well as the junctions where we might get an air leak, using SIGA air-tightness tapes.
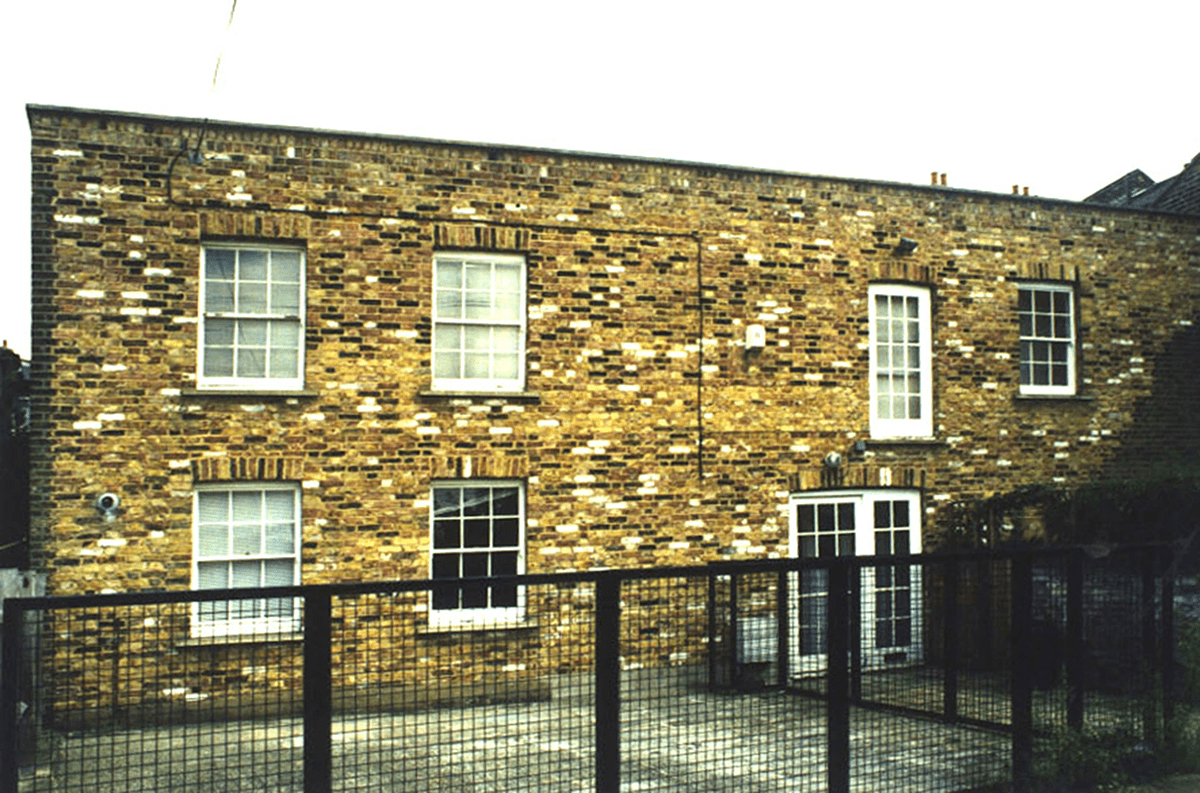
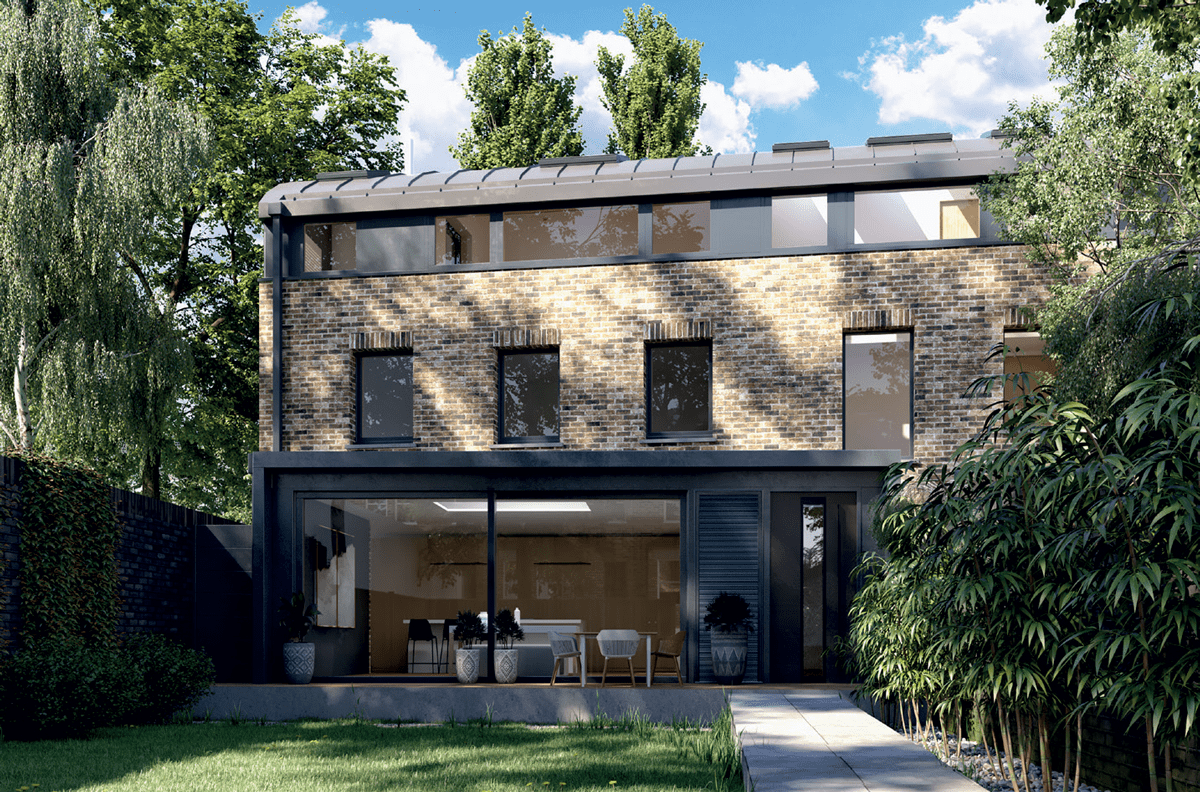
Air tightness tests
We carried out a number of air tests.The first was carried out before the windows were put in and the windows were lined with a DPM membrane to see whether the building was close to getting our achieved level of below 1 n50 p/h air change. The first air test at this stage came in at around 2 n50 p/h. Current building regulations are set to below 10 n50 p/h. This is a good way to check that you are on target.
At this stage we started on the second fix. This involved using armor cell insulation around pipes and ensuring that no air leaks would occur, using smoke tests and thermal imaging cameras. The chosen heating method on the lower floors was underfloor heating as this works at a very low temperature, and a Mitsubishi Ecodan Ultra Quiet heat pump made it a good choice. At any tight corners we ensured that the air tightness was carried out with SIGA tape, ensuring that the building and the frame would be airtight. A steel staircase was placed into the building and the building is now beginning to perform well with an air tightness test of 0.98 n50 p/h, which is a pass for an EnerPhit Passivhaus.
The building itself is beginning to perform well and we are now at the stage of finishing off the second fix, which includes the lighting and finalising the plumbing work. The hot water will be supplied by a Mixergy tank while the Mitsubishi Ecodan Ultra Quiet heat pump will provide enough heat for the building as well as for the hot water. Solar panels will provide around another 5kw of power directly to the hot water tank, which is all centrally managed.
Home comforts
It’s satisfying to achieve ambitious performance targets, but the real satisfaction lies in the tangible improvements to family life.
The Passivhaus home design allows each room to have natural, filtered air giving everyone freedom to breathe easily. My family love the fact that they don’t have to worry about hay fever and their allergies. Even the pollution from London and the soot from the cars won’t affect us in the house.
Inside a Passivhaus, you don’t feel the cold winter of London. There is no draft unless you wish there to be one. You can move from room to room without getting cold chills. With the triple-glazed windows, the Passivhaus design provides immunity from surrounding noise. Heathrow and City airports are nearby, but we are blissfully oblivious to planes flying overhead and cars beeping in the streets.
Credits
Project team
Architect
RDA Architects
Structural engineer
CTD Engineers
Passive house consultant
Ecospheric
Ventilation system design
Paul Heat Recovery
Lighting design
MS Lighting Design
Mist system design
Imist
Passive house certifier
Mead Consulting
Selected subcontractors and suppliers
Waterproofing
Triton Platon P20 and
P8 Delta Dual Sump
Pump
Thermal breaks
Farrat TBK
Timber joists, studs
C24 timber
Curved timber beams
Structural grade
plywood
Window framing system
Iso-top Winframer
“Type 1”
Windows and doors
Josko
Rooflights on flat roof
Roof Maker Passive
House Fixed Flat
Rooflight
Rooflights on barrel roof
Velux GGU
Zinc
VM Zinc
Cold bridge strip
Spacetherm Cold Bridge
Strip
Wood fibre insulation
Steico
PIR insulation
Ecotherm Eco-Versal
(walls)
Celotex GA 4000
(basement floor)
Foam insulation
Illbruck FM330 Pro Foam
Air Seal
Render system
SecilTek Isovit E-Cork
Regency lime plaster
Sprayed/painted
Passive Purple
Airtight membrane
Siga Majrex
Tapes
Siga Fentrim, Sicrall,
Rissan, Wigluv