Hareth Pochee, senior engineer at Max Fordham LLP and author of the net zero report for Max Fordham’s House, answers readers’ questions to explain how the figures behind the UK’s first carbon zero house stack up.
How can this be the first net zero home? It’s only the verification that has changed.
Max Fordham House is the first home to be verified as net zero in line with the UKGBC Net Zero Carbon Building Framework, which requires particular standards to be met and body of evidence to be provided, reviewed and verified.
As is normal in any evolving field of work, needs and approaches change over time, as is the case with net zero carbon buildings. The UKGBC Net Zero Carbon Building Framework (used in conjunction with the RIBA 2030 Climate Challenge and LETI / RIBA Target Alignment documents) aim to provide a contemporary definition and set of requirements for net zero carbon buildings.
Can you discuss the use of air source heat pumps and its energy efficiency?
The Max Fordham house uses an air source heat pump for heating domestic hot water only. Space heating is provided by a single electric resistance heater element in the supply air duct of the whole house MVHR system. Because the building is a Passivhaus, the demand for heat is very low, about 10W/m2 (of floor area). The size of the in-duct heater that heats the whole house is 2kW, about the same as a kettle.
What refrigerant gases were selected for the heat pumps?
The heat pump used at the Max Fordham House is a 2-stage high temperature unit by Daikin. The refrigerants in the units are R134a and R410A, which unfortunately both have high global warming potential (GWP) if they leak into the atmosphere. At the time the house was being designed and constructed, the product choices were very limited for heat pumps that can heat water to temperatures greater than 60°C, which is the temperature needed to control legionella bacteria. There are now many more high temperature heat pumps available on the market, several of which make use of low GWP refrigerants such as propane or CO2.
Embodied carbon modelling analysis carried by Max Fordham LLP on the 20 most contributing products for the Max Fordham House
How does the “off-setting” work? What is this used for?
For Max Fordham House, the total embodied carbon emissions for the whole building at the point of practical completion was calculated to be 102 tCO2e. Two different types of Gold Standard verified carbon offsetting credits were purchased to cover (more than) this quantity of emissions. The specific projects funded were “Planting Biodiverse Forests in Panama” and “100.5 MW Wind Power Project in Madhya Pradesh, India”.
As per the UKGBC requirements, these offsetting credits are ones that meet the highest standard of quality assurance and were of the ex-post type, meaning they are projects that have already happened, rather than ones planned for the future. The only currently available carbon offsetting projects that meet the UKGBC quality requirements for the residual carbon balance are Gold Standard and VCS verified projects, none of which are UK based, hence the international approach taken.
There are many moral and practical questions and challenges relating to offsetting. Our opinion is that whilst not perfect and not a long-term solution, funding high quality offset projects to achieve net zero for embodied carbon emissions is much better than not doing it at all. The key issue is that the initial embodied emissions of the building need to be limited to low values prior to offsetting being considered. The cost of offsetting also needs to be high enough to encourage building owners to prioritise reducing emissions first, which is why the offsetting for Max Fordham House was voluntarily purchased at £70/tonne, far higher than the market rate.
How much did the dwelling cost?
The Bow Tie Construction website states c. £1.25 million.
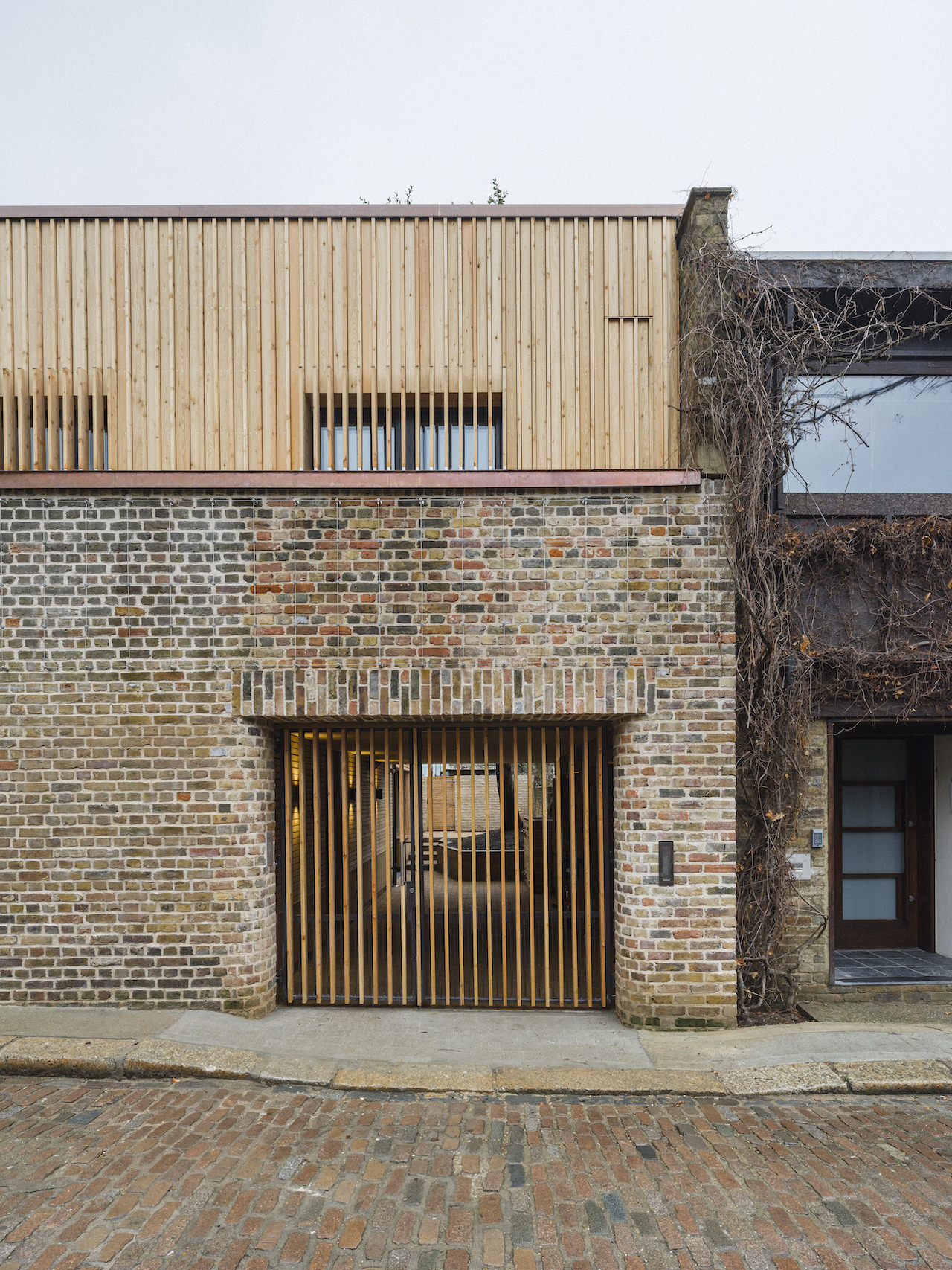
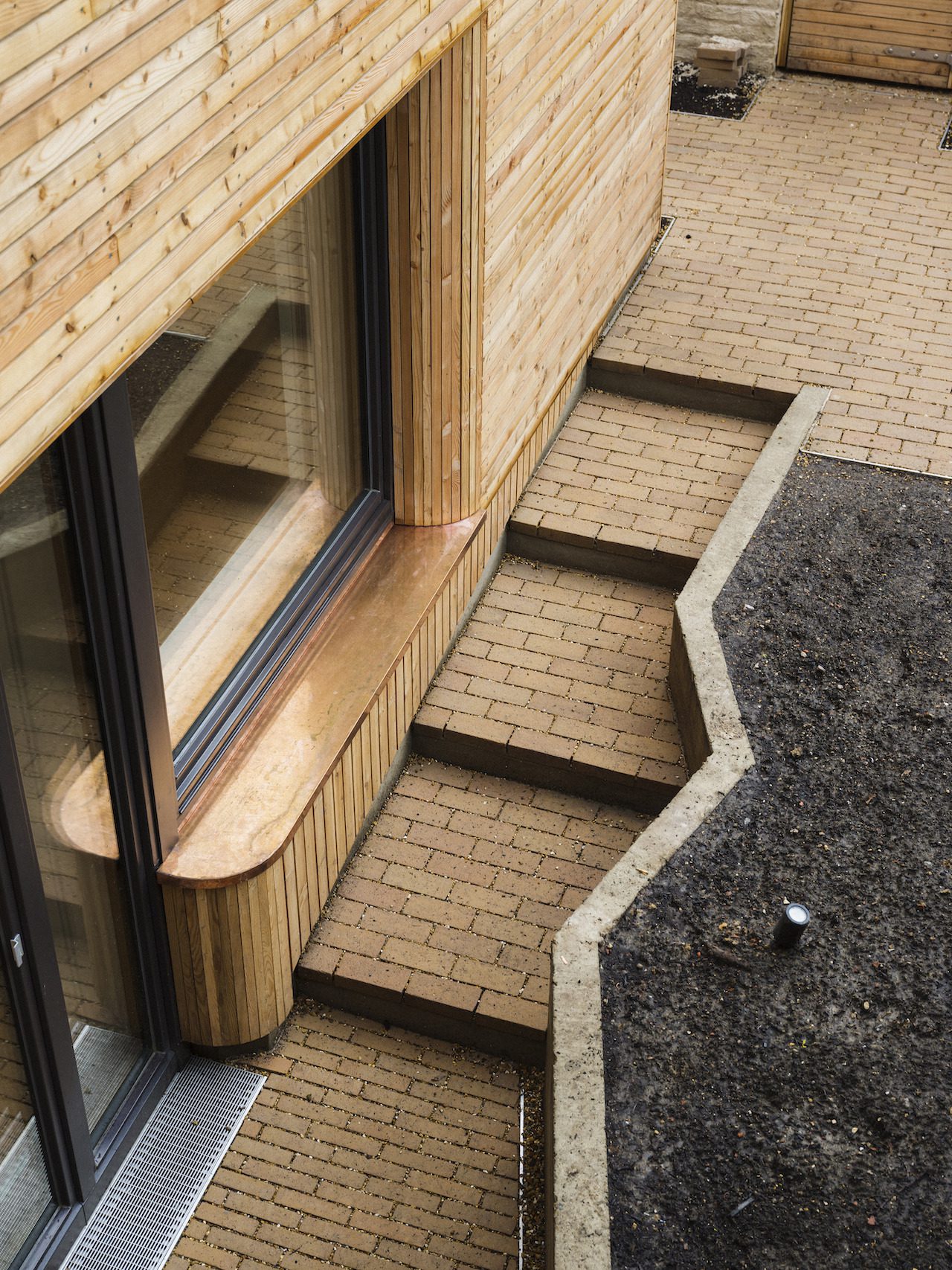
What are the targets meant by “project-specific net zero carbon compatible target of 640kgCO₂e/m² (A1-A5), for residential building’s designed in 2016”?
The UKGBC Levels of Performance (for net zero carbon buildings) document states that in order to achieve net zero in line with the UKGBC Framework, it is required that the building’s upfront embodied carbon emissions calculated from as-built information is lower than a suitable target value. UKGBC doesn’t publish their own target values, they advise to consult publications from third parties such as CRREM, LETI or RIBA.
For the Max Fordham House, we made use of the guidance contained within the Embodied Carbon Target Alignment document published by LETI / RIBA / WLCN / IStructE.
The analysis of this project was somewhat unusual as it was designed and constructed before the LETI / RIBA document was published.
We extrapolated from the published figures for residential buildings to set a Max Fordham House project-specific target of 640kgCO₂e/m² (A1-A5) for the project that was designed in 2016.
The targets given in the LETI / RIBA Embodied Carbon Target Alignment document are actually for blocks of flats. One could argue that the values for individual dwellings could or should be higher.
What about all those UK homes that existed before central heating that were built from locally sourced timber, stone, horse hair and unfired clay?
It is likely that, for similar levels of functionality, comfort and safety, a home built in the 1800s would have five to ten times the annual energy demand (and operational CO2 emissions) of a modern Passivhaus, due to very poor insulation and airtightness. Stoves and fires would have been very inefficient and burnt coal, oil or timber to produce heat and for cooking.
In the past, people didn’t heat their buildings to the extent or temperatures that are required / expected these days. Aspects such as illumination, acoustics, protection against water borne bacteria were, in general of much lower standards in the past than in contemporary buildings. In general, addressing these issues to deliver buildings to modern standards requires more building elements, more sophisticated materials and technologies and more energy.
In terms of the building materials, we can refer to the embodied carbon modelling analysis we carried out of the 20 most contributing products for the Max Fordham House. The results are shown in the graph included above.
If we optimistically assume that an unfired clay brick has zero embodied carbon impact, then replacing the bricks that were used on the project with unfired equivalents would reduce the overall project upfront embodied carbon footprint by about 2%. However, (challenges with the planners aside) most unfired clay bricks are not weather resistant and so an additional layer of something would probably be required which would push the project embodied carbon back up somewhat.
Using horsehair lime plaster (even if assumed to have zero embodied carbon) rather than the specified gypsum plaster would only reduce the project embodied carbon footprint by less than 1%.
The use of timber (whether it be local or imported) seems to have the most promise. The modelling has shown that 40% of the upfront building embodied carbon footprint is due to concrete (including the re-bar), and this is with concrete with 50% GGBS low carbon cement replacement. Using a lightweight timber frame would significantly reduce the amount of concrete required in both the super structure and foundation. The upfront embodied carbon impact of the timber would be much lower but there are some issues; timber constructions often need additional layers to meet required acoustic and fire resistance standards. Overall, we might expect around 25% reduction in project embodied carbon footprint which is certainly significant. However, the major issue is the loss of thermal mass and associated passive cooling capacity. A lightweight timber Max Fordham House would likely require and active cooling system to not overheat in summer.
Given the urgency of the climate emergency, significant reductions in upfront embodied carbon emissions with slightly higher long term operational energy demands might be the right strategy for new buildings.
Hareth Pochee is senior engineer at Max Fordham LLP and author of the net zero report for Max Fordham House